TCT 3SIXTY Trade Show 4th and 5th June 2025
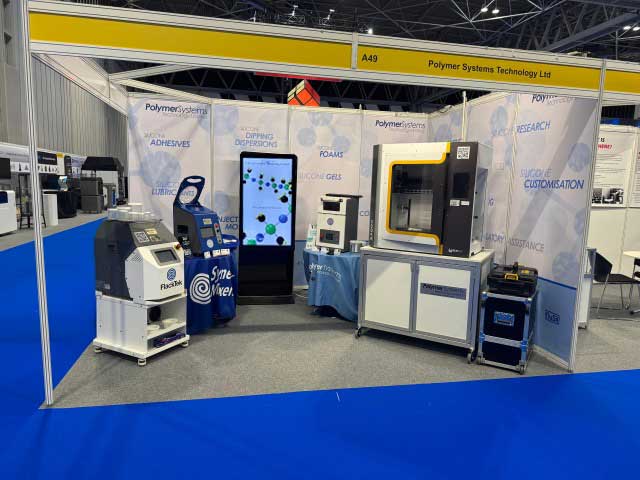
As a key market for PST it’s always good to keep up-to-date with the latest technologies and developments.
Exhibiting and introducing the 3D Printer from Lynxter; we sell both the materials and the equipment.
We were also joined by Synergy, demonstrating their mixer technology for mixing and degassing silicones and other materials.
As always it was a great opportunity to hear about exciting new developments, meet new and old contacts.
Thank you to all who came to visit our stand.